AZS fused cast block is also called fused cast block which is abbreviated as AZS because it contains Al2O3-ZrO2-SiO2. It is made from pure alumina powder and Zircon sand with the addition of a small amount of alkali metal oxides.
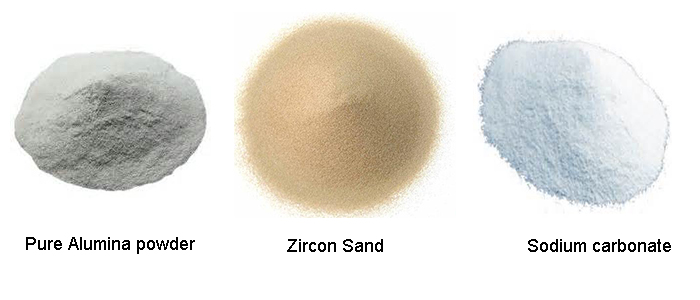
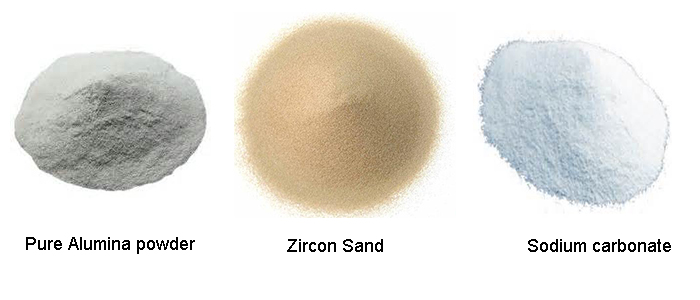
Alumina powder and zircon sand melting in electric furnace, and then the melt is cast into molds and cooled down to become white solid. The AZS products generally contain from 45 to 50% Al2O3, from 32 to 40% ZrO2, from 12 to 16% SiO2 and approximately 1% alkali metal oxides(Na2O, K2O). Because of the different content of Zirconia from 33%-41%, our AZS blocks can be divided into three types AZS—33#,AZS—36# and AZS—41#.
The pure Alumina powder is produced from bauxite with chemical method by removing impurities(Si、Fe、Ti) and calcining it at 1300~1400℃ to produce the pure alumina. Bauxite consist of 40-60% alumina, as well as earth silicon, ferrous oxide, and titanium dioxide. It is the most common raw material used to produce alumina. Al2O3 constitutes corundum crystals. it features high melting point and great wear and corrosion resistance.
Zircon Sand is composed mainly of zirconium silicate ZrO2. The zircon sand used to produce fused cast AZS block composes of 65% zirconia and 34% SiO2. ZrO2 features high melting point and great corrosion resistance to melt glass, so it can improve the corrosion resistance to melt glass.
Desilication zircon sand is used to improve the zircon content to 36%~41% without increasing the SiO2 content. It is produced by removing SiO2 from zircon sand. It contains more than 90% zircon. SiO2 is the main component for forming the network of the matrix glass. Although its existence can help the block exhibit a good structure and prevent it from cracking, mullite is likely to form, and the absolute amount of exudation of the matrix glass tends to increase with the increase of SiO2 content.
For cost reasons, the alkali metal oxide is preferably Na2O due to its low cost. Sodium carbonate is added to produce Na2O. Na2O can constitute a structure for modifying the network of the matrix glass and exhibits an action to control the viscosity of the matrix glass and an action to inhibit the formation of mullite. If the content of Na2O is too low, the formation of mullite is accelerated and the block is apt to crack. However, if it is too much, the superior non-exudation characteristic of matrix glass can not be obtained.