The fused cast AZS block is the most widely used refractories in glass furnaces. It features high temperature resistance and great corrosion resistance to melt glass. Its manufacturing process generally includes melting of the raw materials, casting, cooling and cutting.
Recently oxidation technology is used in manufacturing fused cast AZS, which has greatly improved the quality and performance of AZS. It features high voltage, low pollution, and low carbon content. The oxidation technology greatly improves the corrosion resistance to melt glass and increase the exudation temperature of Glass phase.
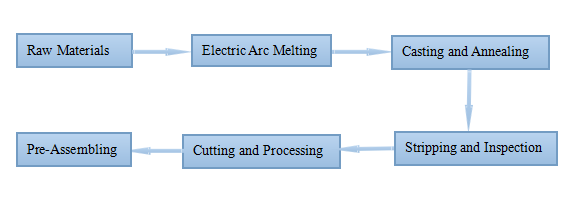
Fused cast AZS block is prepared in such a manner that a mixed material is melted in an arc electric furnace, and the obtained melt is cast into a casting mold, embedded in a heat insulating material, followed by cooling the cast product in alumina powder to form white solid.
The quality of AZS is up to the quality of raw materials and manufacturing technology. One of the raw materials used is pure Al2O3 powder. In China, refractory manufacturers always employ Al2O3 powder from Zhengzhou, Guiyang, Shandong and Australia. Zircon sand(ZrSiO4, composed of 65% zirconia and 34% SiO2) is another raw material. Most of Zircon sand used are from Hainan, Guangdong and Australia.
The quality of the molds has influence in the quality of the final products too. A mold is always formed by silica sand with a binder(sodium silicate, phosphate and phenolic resins) for the sand. The mold must have good permeability, high impact strength, good thermal mechanical strength, accurate dimensions and flat surface.
When casting, it is important to control the casting temperature and casting speed. If it is too rapid, the air in the mold cannot be exhausted, the bottom of the mold may be broken and knots will be formed. If it is too slow, it will increase the casting time and cause uneven surface. Products made with PT casting have bigger voids. Products made with QX, ZWS and WS have smaller voids, but it is costly.
After casting and cooling, the surface of the products is rough and the shape and dimensions are not accurate. It needs to be cut and processed with diamond tools to form the final products.
Pre-assembling refractories have been employed in many applications. It can avoid the defaults assembled at the site, save installation fees and decrease the repair time.